As the largest privately-owned spring manufacturer in North America, with almost 100 years of spring-making knowledge behind us, Peterson American Corporation is uniquely positioned to offer our customers a wide array of spring innovations, customized to meet their individual and specific needs. Years of honing the art of spring making to meet the exacting standards of the automotive and aerospace industries has given our Engineers, Metallurgists and Designers a wealth of experience that cannot be duplicated. From high-end specialized racing valve springs to cost-effective, economically responsible alternatives, Peterson has the expertise to match a spring to fit your exact requirements and the ability to customize a device when proactive design is necessary.
Extension Springs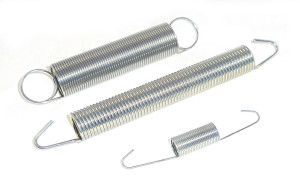
Helical extension springs store energy and exert a pulling force. Extension springs differ from compression springs in that they do not have a solid stop to prevent overloading. For this reason, they are designed with lower stress levels. Typical applications include balance scales, trampolines, garage doors, dock levelers, farm machinery and various types of spring tensioning devices. Extension springs come in a wide array of sizes from small medical devices to off-road machinery brake springs.
In order to be a part of an assembly, extension springs require a method of attachment. Threaded inserts, swivel hooks, twisted loops and side loops are just a few of the nearly limitless options available. At the design stage, the length and positioning of the hooks at each end of the spring can be adjusted in order to obtain exactly the required spring load at any extended position. Silencers can be used to prevent vibration within the spring itself as well as eliminating noise in the application without upsetting the function of the spring.
Peterson Spring specializes in extension springs, using state of the art machinery and world class engineering. Our corporate laboratory, as well as individual plant testing facilities, allow us to fully serve every customer with superior manufacturing, testing data, and metallurgical documentation.
Torsion Springs
Helical springs used to apply a torque or store rotational energy are commonly referred to as “torsion springs” and are typically found in single-and double-bodied forms. Everyday uses include clothespins, ratchets, counterbalance mechanisms, and as a coupling between concentric shafts such as in motor and pump assembly.
Cost-conscious torsion springs implement round wire. When the situation calls for higher performance, rectangular or other non-round wire can be substituted to improve efficiency and obtain higher energy storage capacity. Space between the coils can also be designed to reduce friction. In a case of extreme torque, two separately-designed coil sections – one with a right-hand twist and the other left-handed – can be connected together creating a double-bodied spring. This allows the total torque to match the sum of the two coils combined. Various kinds of ends including short hook, hinge, straight and customizable are available to facilitate mounting.
At Peterson Spring, we not only design, manufacture, and test these springs, we are customer focused to ensure clients are matched with the proper device to suit their needs.
Compression Springs
As one of the most efficient energy storage devices available, helical compression springs are the most common spring configuration in the marketplace today. From automotive engines to major appliances, they are found in countless applications.
Though, they are typically manufactured from round wire in a cylindrical shape, compression springs are extremely customizable. Square, ovate, rectangular and other non-round cross section wire can be fashioned to meet differing requirements. Additionally, the spring can be altered to conical, hourglass or barrel shape among other profiles. In this way, dynamic resonance conditions or height restrictions can be addressed. Variable pitch between the coils provides different spring rates throughout the operating range of the spring and aid in minimizing resonate surging and vibration. Because of the number of compression spring characteristics that can be tailored to specific circumstances, this type of spring represents a flexible design approach to force resistance and energy storage.